Service Contract
Let us take the worry out of your CFR servicing requirements.
Our unique CFR Management Information Software allows predictability for servicing requirements and component replacement.
Using the data collected by our engineers during servicing, we can specifically design the on-going future service requirements unique to that CFR unit, reducing any replication and unnecessary maintenance costs.
The information we collect from a consistent maintenance programme allows us to monitor the wear characteristics of over 42 mechanical measurements and the full range of test method parameters.
This means we will be fully prepared upon arrival at your site to perform only the necessary servicing requirements and ensure that your engines perform at their optimum level at all times.
Each laboratory will be contacted 6 weeks prior to the last service anniversary for information regarding current calibration performance, running hours and other engine issues.
By visiting your sites annually it also allows us to identify available onsite tooling, thereby reducing our engineer’s excess baggage costs.
All work carried out will be supported by a comprehensives set of reports (examples available) to enhance any Quality Assurance Programmes and Audit requirements.
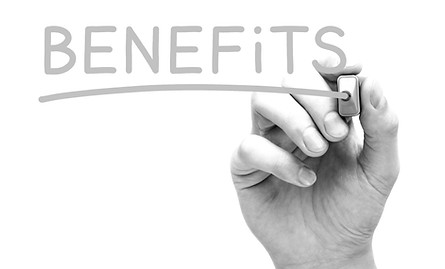
Outlined
- Reduce Corporate Risk
- Independent Verification & Equipment Compliance
- Single Point Technical Support
- Equipment Familiarisation
- Global Fixed Costs
- Tailor Made Servicing – Equipment Unique
- Priority Technical Support
- Laboratory Process / Procedure Evaluation & Support
- Eliminate Expensive Stock Inventory Replication
- Comprehensive Reporting
- Service Reminders Sent Automatically
How it Works
Phase 1
Equipment Registration
Arrange Initial Evaluation & Service
Booking Request Completed
Service & Evaluation Carried Out
Phase 2
Reminder Service & Information Request Sent
Equipment Data Evaluated For Service Type
Arrangement of Service
Booking Request Completed
Service Completed & Service Reports E-mailed